November 15, 2024
Ensuring a Safe Work Environment: Safeguarding Against Injuries and Illness in the Workplace
Every workplace is susceptible to incidents and accidents that can lead to injuries and illnesses. This is why incident reporting and investigation play a critical role in safeguarding employees and maintaining a safe work environment. By uncovering the root causes of incidents, businesses can implement effective preventive measures to avoid future occurrences.
In this article, we will explore the key steps involved in incident reporting and investigation, from collecting accurate data to conducting thorough analysis. Additionally, we will highlight the importance of creating a culture of reporting and how to effectively communicate findings to prevent similar incidents across the organization.
In today's fast-paced work environments, ensuring the safety and well-being of employees is more critical than ever. One major aspect of maintaining a safe workplace is effective incident reporting and investigation. This blog will explore why these processes are essential, how they work, and the best practices for implementation.
Discover the power of incident reporting and investigation and how it can positively impact your organization's safety performance and overall success.
What is Incident Reporting?
Incident reporting refers to the formal process of documenting any unexpected event that has caused or has the potential to cause harm, damage, or disruption within an organization. Incidents can range from minor accidents, such as slips and falls, to more serious occurrences like fires or chemical spills.
Why is Incident Reporting Important?
1. Prevention of Future Incidents: Enables corrective actions to prevent recurrence.
2. Legal Compliance: Many industries are governed by regulations that require prompt reporting of certain types of incidents. Failing to comply can lead to legal penalties.
3. Continuous Improvement: Incident reports provide valuable data that organizations can analyze to enhance safety measures and procedures.
4. Employee Engagement: Encouraging employees to report incidents fosters a culture of safety and responsiveness, leading to quicker resolutions.
- 5. Overall Productivity: Contributes to a safer work environment, improving productivity and well-being.
- Overview of Workplace Injuries and Illness
- Understanding workplace injuries and illnesses is crucial for safety management and regulatory compliance. This informative guide addresses various types of injuries and reporting requirements, focusing on both non-work-related and work-related incidents.
- Non-Work-Related Injuries/Illnesses/Diseases
- These are health issues that occur outside the workplace and do not arise from occupational duties. Examples include:
- Personal injuries from sports activities.
- Illnesses such as influenza or allergies not influenced by workplace conditions.
Work-Related Injuries/Illnesses/Diseases
These are directly linked to an individual's employment and can include:
Lost-Time Injuries (LTIs): Injuries that result in the employee being unable to work for a set period.
Medical Aid Cases: Incidents requiring medical attention but do not result in lost work time
Types of Work-Related Conditions:
1. Occupational Illness: Refers to diseases arising from work-related exposures, such as:
- Asbestosis from asbestos exposure.
- Repetitive strain injuries from repetitive tasks.
2. Workplace Exposure: Situations where employees are exposed to harmful substances or environments, potentially leading to long-term health risks.
Additional Incident Reporting
Certain serious incidents require specific documentation and follow-up reporting to ensure comprehensive safety protocols. These include:
1. Fatality: Any employee death resulting from a workplace incident must be reported.
2. Critical Injury: Severe injuries that could result in permanent disability or life-threatening conditions.
3. Premature or Unexpected Explosion: Incidents involving unplanned explosions affecting any work area.
4. Fire: Any workplace fire incident needs immediate reporting and investigation.
5. Flood or Inrush of Water: Reports should be made for significant water influx that impacts work safety.
6. Violence or Fire: Incidents involving physical violence or aggressive behavior in the workplace should be documented.
7. Equipment Failure: Any malfunction of equipment that endangers employees or disrupts operations.
8. Incident Per Regulation 420/21: Specific incidents outlined under this regulation necessitate detailed reporting.
9. Environmental Spill: Spills of hazardous materials that could harm the environment or public safety must be reported.
10. Motor Vehicle Incidents: Accidents involving company vehicles or while conducting work duties.
11. Psychological Injury Incidents: Situations that may lead to psychological trauma among employees should be closely monitored and reported.
12. Property Damage: Any damage to company property that occurs during work activities needs documentation.
What is Incident Investigation?
The purpose of an incident investigation aims to identify the underlying causes of an incident/ occurrence and implement corrective action to eliminate or reduce the risk of similar incidents happening in the future. This process is crucial for preventing future occurrences and improving overall safety. The incident most likely will be investigated by your companies Health & Safety Manager, Supervisors, Joint Health and Safety Committee (JHSC) and workers (the witnesses).
The Objectives of Incident Investigation
1. Identify Root Causes: Understanding why an incident occurred rather than merely addressing its symptoms.
2. Develop Preventive Measures: Creating actionable solutions to mitigate risks and prevent future incidents.
3. Compliance with Regulations: Ensuring that investigations meet industry standards and regulatory requirements.
4. Documentation for Future Reference: Keeping a record of investigations can inform training programs and policies.
Steps in the Incident Investigation Process
1. Initial Response: Ensure the safety of all personnel and provide necessary medical assistance if needed.
2. Collect Information: Interviewing as soon as possible, one on one interviews with all parties involved, witnesses, other outside experts if needed (suppliers, manufacturers).
3. Scene Assessment: Collect all relevant information, including photographs, equipment involved, site, materials.
4. Identify Contributing Factors:
- People- how many, other trades, location
- Equipment- types and location on site, what were the other pieces of equipment doing at the time
- Product or Material- what was it, location
- Environment- vehicles, weather at the time
- Process- who and what was being done at the time of the incident
5. Writing The Report: Review and analyze various contributing factors such as weather, traffic, personnel, and products, alongside the floor plan or job layout and the time of day. Reviewing training records, the work area, and the availability of safety equipment, highlighting any deficiencies. The most recent Workplace Inspection Form and disciplinary actions will be examined to identify trends.
6. Recommendations for Corrective and Preventative Action: Depending on your company’s course of action and policy, they could Identify opportunities for continuous improvement by your JHSC, assigning responsibilities for corrective action, timeline for corrective action, and monitor progress of what has been done, who did it, and when did it happen.
7. Review and Follow-Up: Once corrective action has been taken, the situation should be monitored by the JHSC to ensure that all corrective actions have taken place and are appropriate. Depending on your JHSC there can be monthly Workplace Inspections will document the progress of the recommendation
In the workplace, injury, illness, and incident reporting are vital for fostering a culture of safety and accountability. These reports help identify hazards, enabling organizations to address risks proactively and prevent future occurrences. Thorough incident investigations play a crucial role in uncovering root causes, allowing for targeted corrective actions that improve safety protocols and practices. This not only protects employees but also promotes a culture of continuous improvement and vigilance. By prioritizing effective reporting and investigation processes, organizations create a safer work environment that benefits everyone, ultimately enhancing productivity and morale.
At ESS, safety is our top priority, underpinning every aspect of our operations and culture. We believe that a secure work environment not only protects our employees but also enhances overall productivity and morale. Our commitment to safety is reflected in our rigorous training programs, comprehensive safety protocols, and continuous monitoring of workplace conditions. By fostering a culture of safety, we empower our team to prioritize their well-being and the well-being of the colleagues, ensuring that everyone returns home safely at the end of the day. This dedication to safety not only safeguards our workforce but also strengthens our reputation as a responsible and caring organization.
Tags
- 175|AT
- Aftermarket
- all-terrain
- autograde
- avetta
- Berco
- Best Managed Companies
- bushings
- Canada's Best Managed Companies
- Case Studies
- Caterpillar
- construction
- continuous improvement
- crane
- cranes
- crusherwearparts
- customer focused
- Deere
- dozer
- dozerblades
- efficient
- environment
- EQUIPMENTWATCH
- Esco
- ESS
- excavator
- Excavator Crawler Medium
- excavator telematics
- face sheild
- FINAL TIER 4 ENGINES
- fire
- fire safety
- FUEL CONSUMPTION
- fuel efficiency
- fuelconsumption
- fuelefficiency
- gnss
- gps
- grade
- grade control
- headandcoldstress
- healthandsafety
- healthandsafetyexcellence
- Heavy Equipment
- heavy lifting
- heavyequipment parts
- heavymachinery
- HEAVYMACHINERY TOOLS
- hybrid
- iCraneTrax
- idler
- imc2.0
- Intelligent Machines
- isn
- ITM
- jobsite
- jobsites
- johndeere
- Komatsu
- Komatsu Dozer
- Komatsu Excavator
- Lattice
- LBX
- lifting
- link belt excavator
- Link-Belt 245 X4 Spin Ace
- Link-Belt Cranes is Pulse 2.0
- linkbelt
- LINKBELTCRANES
- links
- loader
- loaderlips
- lockout and tagout
- loto
- machine
- machinecontrol
- maintenance
- my komatsu
- new excavator
- OEM
- pipe
- predictive maintenance
- preventionofslipsandfalls
- remote care
- rigging
- safestemployers
- safety
- safety glasses
- safety talk
- safetyandeyecontact
- safetyandharness
- safetyatheights
- safetycompliance
- safetyfirst
- safetyhandsignals
- safetyspotting
- safetytalks
- sitech
- slipsandfalls
- smart construction
- SMART QUARRY
- smartconstruction
- telematics
- tier4
- TOOLSAFETY
- topcon
- trackshoes
- trimble
- undercarraige
- undercarriage
- vises
- Volvo
- weir
- wheel loader
- WRENCH
- wsib
SIMILAR BLOGS
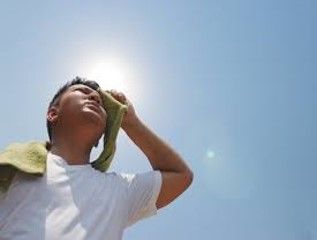
Fire Safety- Most Basic and Most Important!
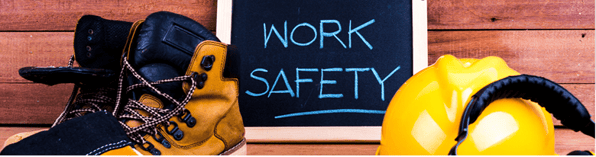
Why are Safety Harnesses Important?
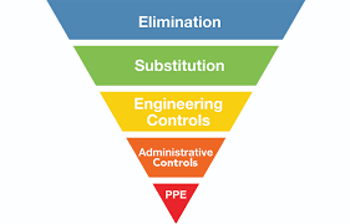
POST YOUR COMMENT